Material, Economic & Geopolitical Consequences
In February 2021, I testified before committees in both the U.S. House and Senate regarding the costs and consequences of replacing the current level of hydrocarbon energy production with wind, solar energy and batteries. Then, in May, the International Energy Agency (IEA), the world’s pre-eminent source of energy information for governments, published a report, “The Role of Critical Minerals in Clean Energy Transitions,”[1]https://www.iea.org/reports/the-role-of-critical-minerals-in-clean-energy-transitions. which supports, in extensive detail, my view that this transition cannot be accomplished anytime soon, that it certainly won’t be “clean,” and that it presents serious geopolitical risks.
To frame my testimony, let me synthesize my introductory remarks to the Congressional committees, which bookend the following presentation.
The increasing use of wind and solar machines is inevitable, even without subsidies, in large measure because of the enormous scale and growth in world demand for energy. Despite significant improvements in energy efficiency in the coming decades, the ongoing digital transformation of society and the economy will alone stimulate more energy demand in America and worldwide—especially in nations with large populations, such as India and Brazil, with fast-growing middle classes that are reaching technological maturity.
Currently, wind and solar supply less than 5 percent of U.S. energy, compared to 84 percent from hydrocarbons. To replace hydrocarbons would entail daunting economic, environmental and geopolitical challenges. While the current federal administration proposes spending $2 trillion on climate programs across seven domains,[2]“The Biden Plan,” https://academized.com/joe-biden-cliimate-plan/. restructuring the electric grid alone would require $5 to $6 trillion in wind/solar and battery systems to replace existing hydrocarbon generation.[3]Philip Rosetti, “What It Costs to Go 100 Percent Renewable,” American Action Forum, January 25, 2019; Dan Shreve, “Deep Decarbonization: The Multi-Trillion Dollar Question,” Wood Mackenzie, … Continue reading
To accomplish this by 2035 would require a continuous construction program at least 600 percent bigger than any single peak year for utility construction that has occurred in the U.S., China or Germany over the past half-century.[4]Michael Cembalest, “Pascal’s Wager,” JP Morgan Asset Management, April 2018. True this would create jobs. However, since the final product remains unchanged but uses more labor and capital, in economic terms, this is the complete inverse of increasing productivity. And, as is widely acknowledged, raising productivity is the single most important feature of an economy that expands overall wealth for citizens.
On top of that, there would need to be an enormous expansion of the grid if a significant share of cars shifts from oil to electricity.[5]Alex Brown, “Electric Cars Will Challenge State Power Grids,” PewTrust.org, Stateline, January 9, 2020. In the end, it bears noting the outcome: Even if a “zero carbon” U.S. grid could be built, it would reduce global carbon emissions by less than 6 percent.[6]EIA, “How Much of U.S. Carbon Dioxide Emissions Are Associated with Electricity Generation?” December 1, 2020.
Grid restructuring and accelerating electric car deployment also means exporting jobs and offshoring environmental consequences. Some 90 percent of solar panels are imported, as are 80 percent of the key components for wind turbines.[7]EIA, “2018 Annual Solar Photovoltaic Module Shipments Report,” July 2019; Ryan Wiser et al., “2018 Wind Technologies Market Report,” U.S. Department of Energy (DOE), Office of Energy … Continue reading Asian companies dominate global battery production and account for 80 percent of all planned factories.[8]Wiser et al., “2018 Wind Technologies Report;” “Global Lithium-Ion Cell Manufacturing Capacity to Quadruple to 1.3 TWh by 2030,” Wood Mackensie, August 11, 2020. Even if we expand domestic manufacturing, our import dependencies remain for critical energy minerals.
On average, per unit of energy delivered, the quantity of materials extracted from the earth and processed for “clean tech” is 500 to 1,000 percent greater than with hydrocarbons.[9]DOE, “Quadrennial Technology Review: An Assessment of Energy Technologies and Research Opportunities,” September 2015. And, as it stands today, Chinese firms dominate the production and processing of many critical rare earth elements, and nearly all the growth in mining is expected offshore, increasingly in fragile, biodiverse wilderness areas.[10]Ashley Stumvoll, “Are There Potential Downsides of Going to 100 Percent Renewable Energy? A New Study Looks at the Danger to Biodiversity that Could Come from Increased Mining of Minerals Used to … Continue reading More mining can be done in an environmentally responsible way, but so far there’s little evidence of support for opening new mines in America.
The Material Cost of “Clean Tech”
The materials extracted from the earth to fabricate everything, including wind turbines, solar panels and batteries (to store grid electricity or power electric vehicles) are typically out of sight, located at remote mine sites and mineral-processing facilities around the world. Those locations matter in terms of geopolitics and supply-chain risks, as well as in general environmental terms and in the accounting of carbon dioxide emissions. The scale of the material demands for building “clean tech” machines is, for many, surprising.
For example, replacing the energy output from a single 100-MW natural gas-fired turbine, itself about the size of a residential house (producing enough electricity for 75,000 homes), requires at least 20 wind turbines, each one about the size of the Washington Monument, occupying some 10 square miles of land.[11]Landon Stevens, “The Footprint of Energy: Land Use of U.S. Electricity Production,” Strata, June 2017. This calculation understates land usage; at least double the number of wind turbines, plus … Continue reading Building those wind machines consumes enormous quantities of conventional materials, such as concrete, steel and fiberglass, along with less common materials, including “rare earth” elements such as dysprosium. A World Bank study noted what every mining engineer knows: “[T]echnologies assumed to populate the clean energy shift … are in fact significantly more material intensive in their composition than current traditional fossil-fuel-based energy supply systems.”[12]Daniele La Porta et al., “The Growing Role of Minerals and Metals for a Low Carbon Future,” Washington, DC: World Banks Group, 2017, p. xii. The new IEA report mentioned at the outset makes the same observation.
All forms of renewable energy require roughly comparable—and enormous—quantities of materials in order to build machines that capture nature’s flows: sun, wind and water. Wind farms come close to matching hydro dams in material consumption, and solar power requires even more. In all three cases, the largest share of the tonnage is found in the use of conventional materials like concrete, steel and glass. Compared with a natural gas power plant, all three require at least 10 times as many total tons mined, moved and converted into machines to deliver the same quantity of energy.[13]DOE, “Quadrennial Technology Review: An Assessment of Energy Technologies and Research Opportunities,” September 2015, p. 390.
For example, building a single 100-MW wind farm—never mind thousands of them—requires some 30,000 tons of iron ore and 50,000 tons of concrete, as well as 900 tons of non-recyclable plastics for the huge blades.[14]Vaclav Smil, “To Get Wind Power You Need Oil,” IEEE Spectrum, February 29, 2016. With solar hardware, the tonnage in cement, steel and glass is 150 percent greater than for wind for the same energy output.[15]DOE, “Quadrennial Technology Review.”
If episodic sources of energy (wind and solar) are to be used to supply power 24/7, even greater quantities of materials will be required. One needs to build additional machines, roughly two to three times as many, in order to produce and store energy when the sun and wind are available for use at times when they are not. Then there are the additional materials required to build electricity storage. For context, a utility-scale storage system sufficient for the above-noted 100-MW wind farm would entail using at least 10,000 tons of Tesla-class batteries.
The handling and processing of such large quantities of materials entails its own energy costs as well as associated environmental implications. But first, the critical supply-chain issue is not so much the increase in the use of common (though energy-intensive) materials such as concrete and glass. The key challenge for the supply chain and the environment reside with the need for radical increases in the quantities of a wide variety of so-called “energy materials.”
The world currently mines about 7,000 tons per year of neodymium for example, one of numerous key elements used in fabricating the electrical systems for wind turbines. Current clean-energy scenarios imagined by the World Bank (and many others) will require a 1,000 to 4,000 percent increase in the neodymium supply in the coming several decades.[16]La Porta et al., “The Growing Role of Minerals and Metals.” Where there are differing underlying assumptions used in various analyses of mineral requirements for green energy, all reach the same range of conclusions. For example, the mining of indium, used in fabricating electricity-generating solar semiconductors, will need to increase as much as 8,000 percent. The mining of cobalt for batteries will need to grow 300 to 800 percent.[17]Matt Bohlsen, “Cobalt Miners News for the Month of November 2019,” Seeking Alpha, November 26, 2019; John Petersen, “The Cobalt Cliff Will Crush Tesla’s Business and May Restore Some Sanity … Continue reading Lithium production, used for electric cars (never mind the grid), will need to rise more than 2,000 percent.[18]Jamie Smyth, “BHP Positions Itself at Centre of Electric-Car Battery Market,” Financial Times, August 9, 2017. The Institute for Sustainable Futures at the University of Technology Sydney last year analyzed 14 metals essential to building clean-tech machines, concluding that the supply of elements such as nickel, dysprosium and tellurium will need to increase 200 to 600 percent.[19]Elsa Dominish, Sven Teske and Nick Florin, “Responsible Minerals Sourcing for Renewable Energy,” Institute for Sustainable Futures, University of Technology Sydney, 2019.
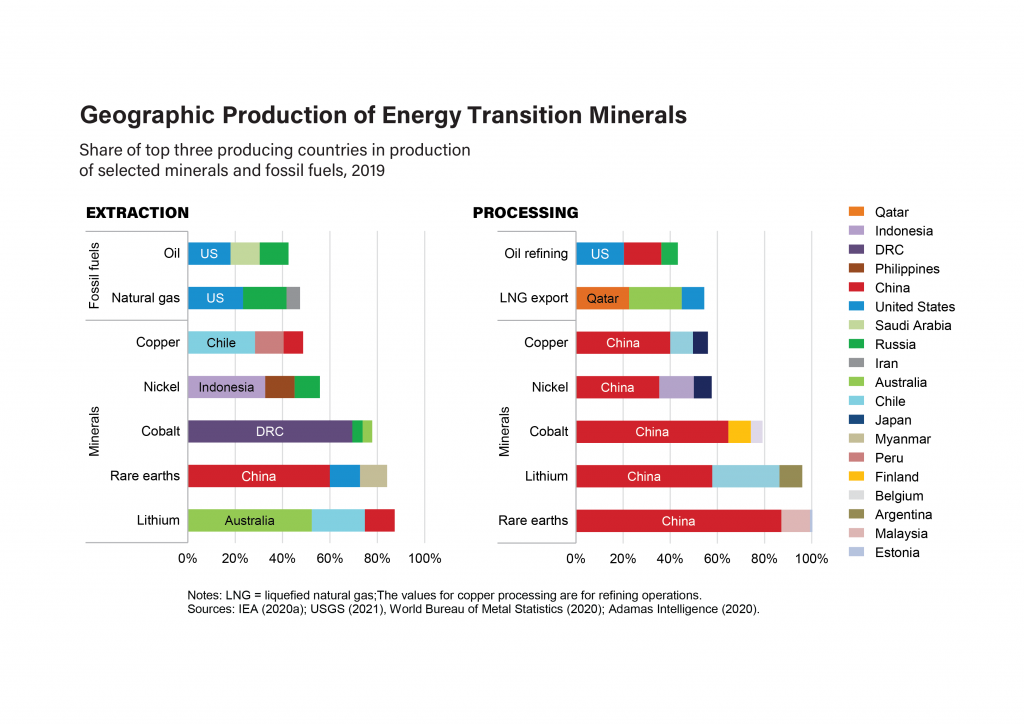
The implications of such remarkable increases in the demand for energy minerals have not been entirely ignored, at least in Europe. A Dutch government-sponsored study concluded that the Netherlands’ green ambitions alone would consume a major share of global minerals. “Exponential growth in [global] renewable energy production capacity,” the study noted, “is not possible with present-day technologies and annual metal production.”[20]Pieter van Exter et al., “Metal Demand for Renewable Electricity Generation in the Netherlands: Navigating a Complex Supply Chain,” Metabolic, Universitiet Leiden, and Copper8, 2018.
Behind the Scenes: Ore Grades & “Overburden”
The scale of these material demands understates the total tonnage of earth that is necessarily moved and processed, all of which requires the use of energy-consuming machines and processes. Forecasts of future mineral demands focus on counting the quantity of refined, pure elements needed—but not the overall amount of earth that must be dug up, moved and processed.
For every ton of a purified element, a far greater tonnage of ore must be physically moved and processed. That is the reality for all elements, expressed by geologists as an ore grade: the percentage of the rock that contains the sought-after element. While ore grades vary widely, copper ores typically contain about a half-percent, by weight, of the element itself: thus, roughly 200 tons of ore are dug up, moved, crushed and processed to get to one ton of copper. For rare earths, some 20 to 160 tons of ore are mined per ton of the element.[21]Laura Talens Peiró and Gara Villalba Méndez, “Material and Energy Requirement for Rare Earth Production,” Journal of the Minerals, Metals & Materials Society (JOM) 65, no. 10 (August 2013): … Continue reading For cobalt, roughly 1,500 tons of ore are mined to get to one ton of the element.
In the calculus of economic and environmental costs, one must also include the so-called overburden—the tons of rocks and dirt that are first removed to get access to the buried mineral-bearing ore. While overburden ratios also vary widely, it is common to see three to seven tons of earth to get access to one ton of ore.[22]McArthur River Mine (Glencore), “Overburden,” 2020.
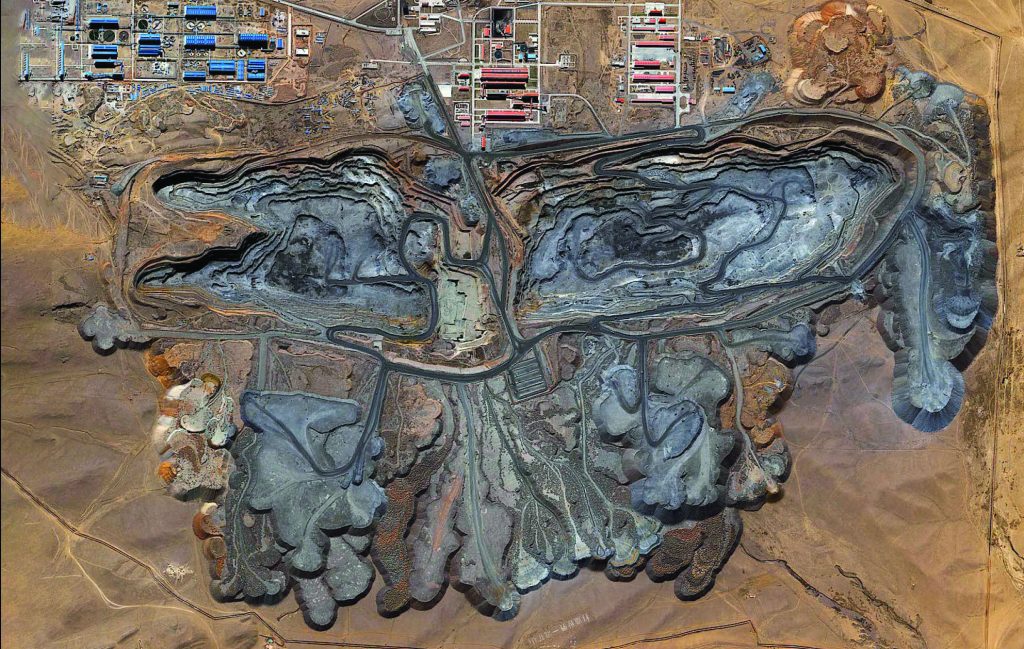
For a snapshot of what all this points to regarding the total materials footprint of the green energy path, consider the supply chain for a single electric car battery, which in final form weighs about 1,000 pounds.[23]A Tesla 85 kWh battery pack weighs 1,200 lbs.: Neil Brooks, “Tesla Battery Weight Overview—All Models,” enrg.io, January 20, 2020. Providing the refined materials needed to fabricate a single EV battery requires the mining, moving and processing of more than 500,000 pounds of materials somewhere on the planet.[24]There is, over the lifespan of a conventional car, 50,000 pounds of cumulative gasoline consumption (counting upstream coproduction of associated liquids). That’s 20 times more than the 25,000 pounds of petroleum that an internal combustion engine uses over the life of a car.
Providing the refined materials needed to fabricate a single EV battery requires the mining, moving and processing of more than 500,000 pounds of materials somewhere on the planet.
The core issue here for a green energy future is not whether there are enough elements in the earth’s crust to meet demand; there are. Most elements are quite abundant, and nearly all are far more common than gold. Obtaining sufficient quantities of nature’s elements, at a price that markets can tolerate, is fundamentally determined by the technology and access to the land where they are buried. The latter is mainly about government permissions.
However, as the World Bank cautions, the materials implications of a “clean tech” future creates “a new suite of challenges for the sustainable development of minerals and resources.”[25]La Porta et al., “The Growing Role of Minerals and Metals.” Some minerals are difficult to obtain for technical reasons inherent in the geophysics. It is in the underlying physics of extraction and physical chemistry of refinement that we find the realities of unsustainable green energy at the scales that many propose.
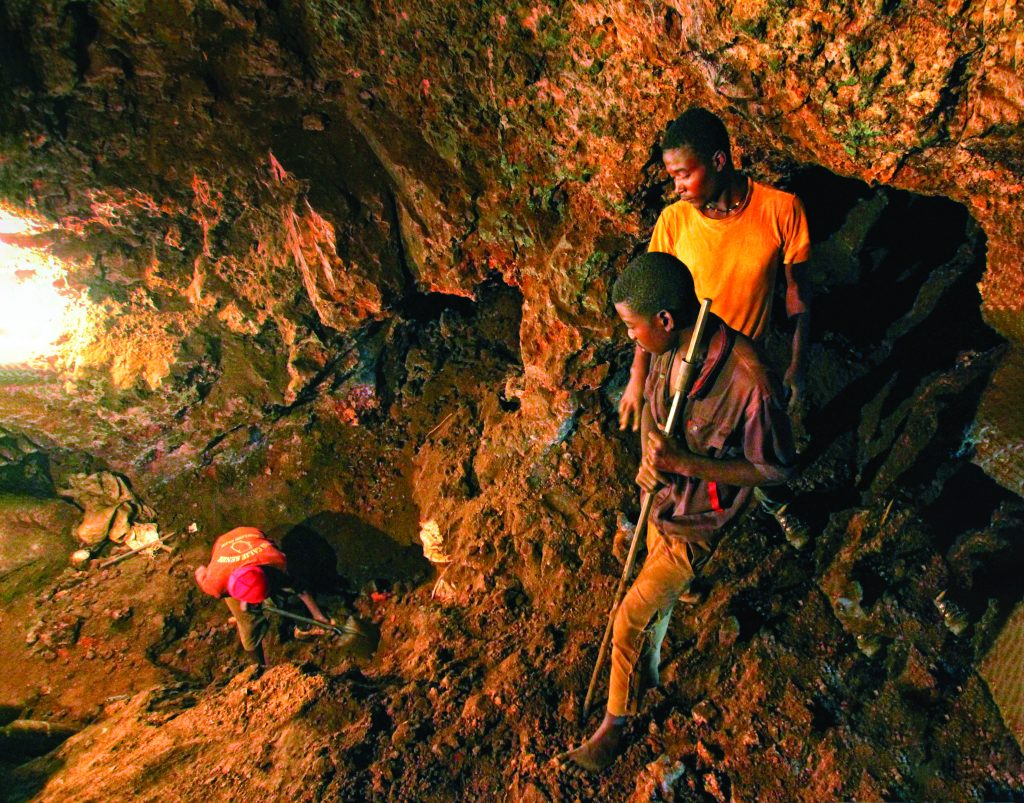
Sources of Minerals: Conflicts and Dependencies
The critical, and even vital, roles of specific minerals have long been a concern of some analysts and various government commissions over the years. One can trace a straight line from an electric car to Inner Mongolia’s massive Bayan Obo mines (for rare earths) and to mines in the Democratic Republic of Congo (for cobalt in batteries). Both of those regions represent the world’s largest supply of rare earths and cobalt, respectively.[26]Hong-Rui Fan et al., “The Giant Bayan Obo REE-Nb-Fe Deposit, China: Controversy and Ore Genesis,” Geoscience Frontiers 7, no. 3 (May 2016): 335-44; DOI and USGS, “Mineral Commodity Summaries … Continue reading
Politically troubled Chile has the world’s greatest lithium resources, although stable Australia is the world’s biggest supplier. Elsewhere in the battery supply chain, Chinese cobalt refiners have quietly gained control over more than 90 percent of the battery industry’s cobalt refining, without which the raw cobalt ore is useless.[27]John Petersen, “The Cobalt Cliff Could Eradicate Non-Chinese EV Manufacturing Before 2030,” Seeking Alpha, July 3, 2019.
The Institute for Sustainable Futures cautions that a global gold rush for green minerals to meet ambitious plans could take miners into “some remote wilderness areas [that] have maintained high biodiversity because they haven’t yet been disturbed.”[28]Stumvoll, “Are There Potential Downsides of Going to 100 Percent Renewable Energy?” And then there are the widely reported cases of abuse and child labor in mines in the Congo, where 70 percent of the world’s raw cobalt originates.[29]Douglas Broom, “The Dirty Secret of Electric Vehicles,” World Economic Forum, March 27, 2019.
Late in 2019, Apple, Google, Tesla, Dell and Microsoft found themselves accused, in a lawsuit filed in a U.S. federal court, of exploiting child labor in the Congo.[30]Jennifer Smith, “Apple, Goggle, Tesla, Microsoft and Dell Are Accused of Exploiting Child Labor in the Democratic Republic of Congo by African Families Whose Kids Have Been ‘Maimed or Killed’ … Continue reading Similar connections can be made to labor abuses associated with copper, nickel or niobium mines around the word.[31]Kate Hodal, “‘Most Renewable Energy Companies’ Linked with Claims of Abuses in Mines,” The Guardian, September 5, 2016. While there is nothing new about such real or alleged abuses, what is new is the rapid growth and enormous prospective demand for tech’s minerals and green energy minerals. The Dodd-Frank Act of 2010 includes reporting requirements on trade in “conflict minerals.” A recent Government Accountability Office (GAO) report notes that more than a thousand companies filed conflict minerals disclosures with the Securities and Exchange Commission, per Dodd-Frank.[32]GAO, “Conflict Minerals: 2018 Company Reports on Mineral Sources Were Similar in Number and Content to Those Filed in the Prior 2 Years,” September 2019.
Automakers building electric cars have joined smart-phone makers in such pledges for “ethical sourcing” of minerals.[33]Andreas Cremer, “Automakers Pledge Ethical Minerals Sourcing for Electric Cars,” Reuters, November 29, 2017. Car batteries, however, create the biggest demand for “conflict” cobalt.[34]Vivienne Walt and Sebastian Meyer, “Blood, Sweat and Batteries,” Fortune, August 23, 2018. Companies can make pledges; but unfortunately, the record suggests that there is little correlation between such pledges and the frequency of (claimed) abuses in foreign mines.[35]Hodal, “‘Most Renewable Energy Companies’ Linked with Claims of Abuses in Mines.” In addition to moral questions about exporting the environmental and labor challenges of mineral extraction, the strategic challenges of supply chains are a top security concern as well.
Strategic Dependencies: Old Security Worries Reanimated
Supply-chain worries about critical minerals during World War I prompted Congress to establish, in 1922, the Army and Navy Munitions Board to plan for supply procurement, listing 42 strategic and critical materials. This was followed by the Strategic Materials Act of 1939. By World War II, some 15 critical minerals had been stockpiled, six of which were released and used during the war. The 1939 act has been revised twice, in 1965 and 1979, and amended in 1993 to specify that the purpose of that act was for national defense only.[36]National Research Council, Managing Materials for a Twenty-First Century Military, 2008. https://www.nap.edu/catalog/12028/managing-materials-for-a-twenty-first-century-military.
As recently as 1990, the U.S. was the world’s number-one producer of minerals. It is in seventh place today.[37]National Mining Association (NMA), “U.S. Mines to Markets,” 2014. More relevant, as the United States Geological Survey (USGS) has noted, is our strategic dependency on specific critical minerals. In 1954, the U.S. was 100 percent dependent on imports for eight minerals.[38]USGS, “Risk and Reliance: The U.S. Economy and Mineral Resources,” April 12, 2017. Today, the U.S. is 100 percent reliant on imports for 17 minerals and depends on imports for over 50 percent of 28 widely used minerals. China is a significant source for half of those 28 minerals.[39]DOI and USGS, “Mineral Commodity Summaries 2020.”
The Department of Defense and the Department of Energy (DOE) have issued reports on critical mineral dependencies many times over the decades. In 2010, DOE issued the Critical Materials Strategy; in 2013, DOE formed the Critical Materials Institute, the same year the National Science Foundation launched a critical-materials initiative.[40]GAO, “Strengthened Federal Approach Needed to Help Identify and Mitigate Supply Risks for Critical Raw Materials,” September 2016. In 2018, USGS identified a list of 35 minerals as critical to security of the nation.[41]USGS, “Interior Releases 2018’s Final List of 35 Minerals Deemed Critical to U.S. National Security and the Economy,” May 18, 2018.
But decades of warnings about rising mineral dependencies have yielded no significant changes in domestic policies. The reality is that depending on imports for small quantities of minerals used in vital military technologies can be reasonably addressed by building domestic stockpiles, a solution as ancient as mining itself. However, today’s massive domestic and global push for clean-tech energy cannot be addressed with small stockpiles. The options are to accept more strategic dependency or to increase domestic mining.[42]Dave Keating, “Europe Waking up to Raw Materials ‘Criticality,’“ EURACTIV, December 11, 2019. And both those options have unaccounted-for implications for total fuel-cycle carbon dioxide emissions.
Carbon Displacement
The realities of the world mean that using wind, solar and batteries to attempt the wholesale replacement of hydrocarbons over the next few decades would achieve only minor reductions in carbon dioxide emissions. And it would come at enormous environmental, economic and geopolitical costs.
It would result in a tenfold increase in the quantity of materials mined and processed per unit of energy delivered. The U.S. would fall from self-sufficiency in energy production to become a major importer of the critical materials needed to fabricate wind and solar machines and batteries. This would have serious economic consequences in terms of lost businesses and jobs, as well as massive increases in energy costs.
[R]eplacing combustion engines with electrical vehicles in America displaces rather than eliminates global carbon emissions.
And, rather than reducing carbon emissions significantly, the U.S. would be exporting them offshore. A majority of the manufacturing of battery materials and components, for example, occurs in China, where the electric grid is 60 percent coal-fired. Thus, replacing combustion engines with electrical vehicles in America displaces rather than eliminates global carbon emissions.
Mark Mills is a Manhattan Institute Senior Fellow, a Faculty Fellow in the McCormick School of Engineering at Northwestern University and a cofounding partner at Cottonwood Venture Partners, focused on digital energy technologies. Mills is a regular contributor to Forbes.com and writes for numerous publications, including City Journal, The Wall Street Journal, USA Today and Real Clear. Early in Mills’ career, he was an experimental physicist and development engineer in the fields of microprocessors, fiber optics and missile guidance. Mills served in the White House Science Office under President Ronald Reagan and later co-authored a tech investment newsletter. He is the author of Digital Cathedrals and Work in the Age Robots. In 2016, Mills was awarded the American Energy Society’s Energy Writer of the Year. On October 5, 2021, Encounter Books will publish Mills’ latest book, The Cloud Revolution: How the Convergence of New Technologies Will Unleash the Next Economic Boom and A Roaring 2020s.
References
↑1 | https://www.iea.org/reports/the-role-of-critical-minerals-in-clean-energy-transitions. |
---|---|
↑2 | “The Biden Plan,” https://academized.com/joe-biden-cliimate-plan/. |
↑3 | Philip Rosetti, “What It Costs to Go 100 Percent Renewable,” American Action Forum, January 25, 2019; Dan Shreve, “Deep Decarbonization: The Multi-Trillion Dollar Question,” Wood Mackenzie, June 27, 2019. |
↑4 | Michael Cembalest, “Pascal’s Wager,” JP Morgan Asset Management, April 2018. |
↑5 | Alex Brown, “Electric Cars Will Challenge State Power Grids,” PewTrust.org, Stateline, January 9, 2020. |
↑6 | EIA, “How Much of U.S. Carbon Dioxide Emissions Are Associated with Electricity Generation?” December 1, 2020. |
↑7 | EIA, “2018 Annual Solar Photovoltaic Module Shipments Report,” July 2019; Ryan Wiser et al., “2018 Wind Technologies Market Report,” U.S. Department of Energy (DOE), Office of Energy Efficiency & Renewable Energy, August 2019. |
↑8 | Wiser et al., “2018 Wind Technologies Report;” “Global Lithium-Ion Cell Manufacturing Capacity to Quadruple to 1.3 TWh by 2030,” Wood Mackensie, August 11, 2020. |
↑9 | DOE, “Quadrennial Technology Review: An Assessment of Energy Technologies and Research Opportunities,” September 2015. |
↑10 | Ashley Stumvoll, “Are There Potential Downsides of Going to 100 Percent Renewable Energy? A New Study Looks at the Danger to Biodiversity that Could Come from Increased Mining of Minerals Used to Create Batteries for Renewable Energy Technologies,” Pacific Standard, June 20, 2019. |
↑11 | Landon Stevens, “The Footprint of Energy: Land Use of U.S. Electricity Production,” Strata, June 2017. This calculation understates land usage; at least double the number of wind turbines, plus storage, would be needed to replace the continuous availability of electricity from conventional generation. |
↑12 | Daniele La Porta et al., “The Growing Role of Minerals and Metals for a Low Carbon Future,” Washington, DC: World Banks Group, 2017, p. xii. |
↑13 | DOE, “Quadrennial Technology Review: An Assessment of Energy Technologies and Research Opportunities,” September 2015, p. 390. |
↑14 | Vaclav Smil, “To Get Wind Power You Need Oil,” IEEE Spectrum, February 29, 2016. |
↑15 | DOE, “Quadrennial Technology Review.” |
↑16, ↑25 | La Porta et al., “The Growing Role of Minerals and Metals.” |
↑17 | Matt Bohlsen, “Cobalt Miners News for the Month of November 2019,” Seeking Alpha, November 26, 2019; John Petersen, “The Cobalt Cliff Will Crush Tesla’s Business and May Restore Some Sanity to the EV Industry,” Seeking Alpha, September 29, 2019. |
↑18 | Jamie Smyth, “BHP Positions Itself at Centre of Electric-Car Battery Market,” Financial Times, August 9, 2017. |
↑19 | Elsa Dominish, Sven Teske and Nick Florin, “Responsible Minerals Sourcing for Renewable Energy,” Institute for Sustainable Futures, University of Technology Sydney, 2019. |
↑20 | Pieter van Exter et al., “Metal Demand for Renewable Electricity Generation in the Netherlands: Navigating a Complex Supply Chain,” Metabolic, Universitiet Leiden, and Copper8, 2018. |
↑21 | Laura Talens Peiró and Gara Villalba Méndez, “Material and Energy Requirement for Rare Earth Production,” Journal of the Minerals, Metals & Materials Society (JOM) 65, no. 10 (August 2013): 1327-40. |
↑22 | McArthur River Mine (Glencore), “Overburden,” 2020. |
↑23 | A Tesla 85 kWh battery pack weighs 1,200 lbs.: Neil Brooks, “Tesla Battery Weight Overview—All Models,” enrg.io, January 20, 2020. |
↑24 | There is, over the lifespan of a conventional car, 50,000 pounds of cumulative gasoline consumption (counting upstream coproduction of associated liquids). |
↑26 | Hong-Rui Fan et al., “The Giant Bayan Obo REE-Nb-Fe Deposit, China: Controversy and Ore Genesis,” Geoscience Frontiers 7, no. 3 (May 2016): 335-44; DOI and USGS, “Mineral Commodity Summaries 2020.” |
↑27 | John Petersen, “The Cobalt Cliff Could Eradicate Non-Chinese EV Manufacturing Before 2030,” Seeking Alpha, July 3, 2019. |
↑28 | Stumvoll, “Are There Potential Downsides of Going to 100 Percent Renewable Energy?” |
↑29 | Douglas Broom, “The Dirty Secret of Electric Vehicles,” World Economic Forum, March 27, 2019. |
↑30 | Jennifer Smith, “Apple, Goggle, Tesla, Microsoft and Dell Are Accused of Exploiting Child Labor in the Democratic Republic of Congo by African Families Whose Kids Have Been ‘Maimed or Killed’ Mining Cobalt to be Used in Lithium Batteries,” Daily Mail, December 16, 2019. |
↑31 | Kate Hodal, “‘Most Renewable Energy Companies’ Linked with Claims of Abuses in Mines,” The Guardian, September 5, 2016. |
↑32 | GAO, “Conflict Minerals: 2018 Company Reports on Mineral Sources Were Similar in Number and Content to Those Filed in the Prior 2 Years,” September 2019. |
↑33 | Andreas Cremer, “Automakers Pledge Ethical Minerals Sourcing for Electric Cars,” Reuters, November 29, 2017. |
↑34 | Vivienne Walt and Sebastian Meyer, “Blood, Sweat and Batteries,” Fortune, August 23, 2018. |
↑35 | Hodal, “‘Most Renewable Energy Companies’ Linked with Claims of Abuses in Mines.” |
↑36 | National Research Council, Managing Materials for a Twenty-First Century Military, 2008. https://www.nap.edu/catalog/12028/managing-materials-for-a-twenty-first-century-military. |
↑37 | National Mining Association (NMA), “U.S. Mines to Markets,” 2014. |
↑38 | USGS, “Risk and Reliance: The U.S. Economy and Mineral Resources,” April 12, 2017. |
↑39 | DOI and USGS, “Mineral Commodity Summaries 2020.” |
↑40 | GAO, “Strengthened Federal Approach Needed to Help Identify and Mitigate Supply Risks for Critical Raw Materials,” September 2016. |
↑41 | USGS, “Interior Releases 2018’s Final List of 35 Minerals Deemed Critical to U.S. National Security and the Economy,” May 18, 2018. |
↑42 | Dave Keating, “Europe Waking up to Raw Materials ‘Criticality,’“ EURACTIV, December 11, 2019. |